Plastic extrusion for intricate profiles and custom designs
Plastic extrusion for intricate profiles and custom designs
Blog Article
Recognizing the Basics and Applications of Plastic Extrusion in Modern Production
In the world of modern production, the method of plastic extrusion plays a critical duty. Unwinding the principles of this procedure reveals the real adaptability and potential of plastic extrusion.
The Basics of Plastic Extrusion Process
While it might show up complex, the basics of the plastic extrusion procedure are based on reasonably uncomplicated principles. It is a manufacturing process where plastic is thawed and after that shaped into a constant account through a die. The raw plastic product, typically in the type of pellets, is fed into an extruder. Inside the extruder, the plastic is subjected to warmth and pressure, triggering it to thaw. The molten plastic is after that required via a shaped opening, called a die, to form a long, continual item. The extruded item is cooled down and afterwards cut to the desired size. The plastic extrusion process is extensively used in different sectors because of its cost-effectiveness, convenience, and efficiency.
Different Sorts Of Plastic Extrusion Methods
Structure upon the standard understanding of the plastic extrusion procedure, it is essential to discover the numerous strategies entailed in this production method. In contrast, sheet extrusion develops huge, flat sheets of plastic, which are usually further processed into products such as food packaging, shower curtains, and automobile components. Understanding these techniques is vital to using plastic extrusion efficiently in contemporary manufacturing.

The Function of Plastic Extrusion in the Automotive Industry
An overwhelming bulk of parts in modern-day automobiles are items of the plastic extrusion process. Plastic extrusion is primarily used in the production of numerous car components such as bumpers, grills, door panels, and dashboard trim. Thus, plastic extrusion plays a crucial role in vehicle production.
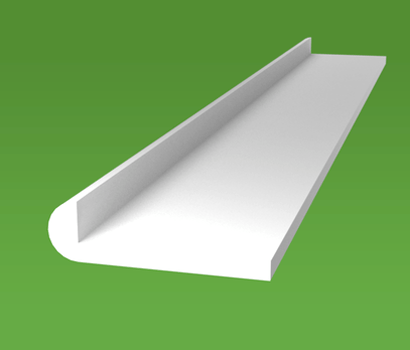
Applications of Plastic Extrusion in Durable Goods Manufacturing
Beyond its significant influence on the automobile market, plastic extrusion verifies just as efficient in the world of durable goods manufacturing. This procedure is vital in developing a vast selection of products, from food product packaging to house devices, playthings, and even medical tools. The versatility of plastic extrusion permits manufacturers to design and produce complicated forms and sizes with high precision and efficiency. Additionally, because of the recyclability of lots of plastics, extruded components can be recycled, lowering waste and price. The adaptability, versatility, and cost-effectiveness of plastic extrusion make it a recommended option for numerous durable goods manufacturers, adding significantly to the industry's growth and advancement. However, the environmental implications of this prevalent use need cautious consideration, a topic to important site be discussed further in the succeeding area.
Environmental Effect and Sustainability in Plastic Extrusion
The pervasive usage of plastic extrusion in making welcomes examination of its eco-friendly ramifications. As a process that often uses non-biodegradable materials, the ecological influence linked here can be substantial. Power intake, waste production, and carbon discharges are all worries. Industry developments are raising sustainability. Reliable machinery lowers power usage, while waste monitoring systems recycle scrap plastic, lowering basic material needs. In addition, the development of biodegradable plastics offers a more ecologically friendly alternative. Regardless of these renovations, better development is needed to reduce the environmental impact of plastic extrusion. As culture leans in the direction of sustainability, makers need to adjust to continue to be practical, highlighting the value of constant research study and improvement in this area.
Verdict
In conclusion, plastic extrusion plays a crucial duty in modern manufacturing, specifically in the vehicle and customer goods fields. Comprehending the essentials of this process is vital to maximizing its advantages and applications.
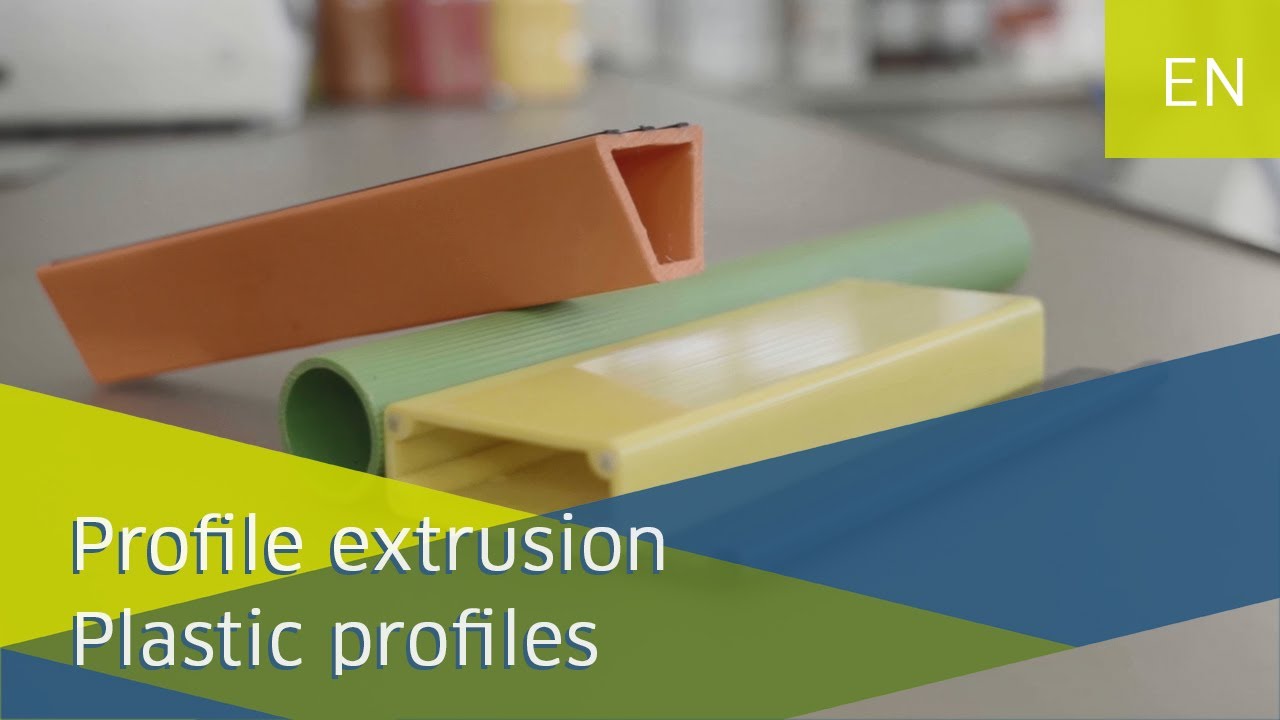
The plastic extrusion process is extensively made use of in various industries due to its effectiveness, cost-effectiveness, and flexibility.
Structure upon the basic understanding of the plastic extrusion procedure, it is necessary to discover the different techniques entailed in this production method. plastic extrusion. In contrast, sheet extrusion creates big, flat sheets of plastic, which are typically additional processed into products such as food product packaging, shower visit this page curtains, and cars and truck parts.An overwhelming bulk of components in modern-day lorries are items of the plastic extrusion process
Report this page